Understanding Component Obsolescence in Manufacturing
Component obsolescence has become a pressing concern for manufacturers and suppliers across various industries. As technology advances rapidly, electronic components are often phased out or replaced, leading to potential challenges in production and supply chain management. The component lifecycle management approach can help navigate these challenges by providing structured methodologies to manage the lifecycle of a component effectively.
The impact of component obsolescence can be severe. For instance, it can lead to production delays, increased costs, and challenges in sourcing replacement parts. According to a recent survey, approximately 50% of manufacturers experienced disruptions in the supply chain due to obsolete components, demonstrating the need for effective strategies in managing components throughout their lifecycle.
The Importance of Component Lifecycle Management
Component lifecycle management (CLM) is an essential practice for manufacturers and suppliers aiming to mitigate the risks associated with obsolescence. It involves tracking, managing, and optimizing the use of components throughout their lifecycle, from initial design to end-of-life phases. The key benefits of CLM include:
- Risk Mitigation: By understanding the lifecycle of each component, manufacturers can proactively address potential obsolescence issues.
- Cost Control: CLM helps in budgeting by forecasting the potential costs associated with replacement and re-engineering.
- Supply Chain Optimization: Keeping an eye on component vendors and their product life cycles can streamline procurement processes.
Components Lifecycle Phases
To effectively manage component obsolescence, it’s crucial to understand the different phases of the component lifecycle. Each phase requires targeted strategies to maximize product efficiency and reduce obsolescence risks. The primary phases are:
1. Introduction
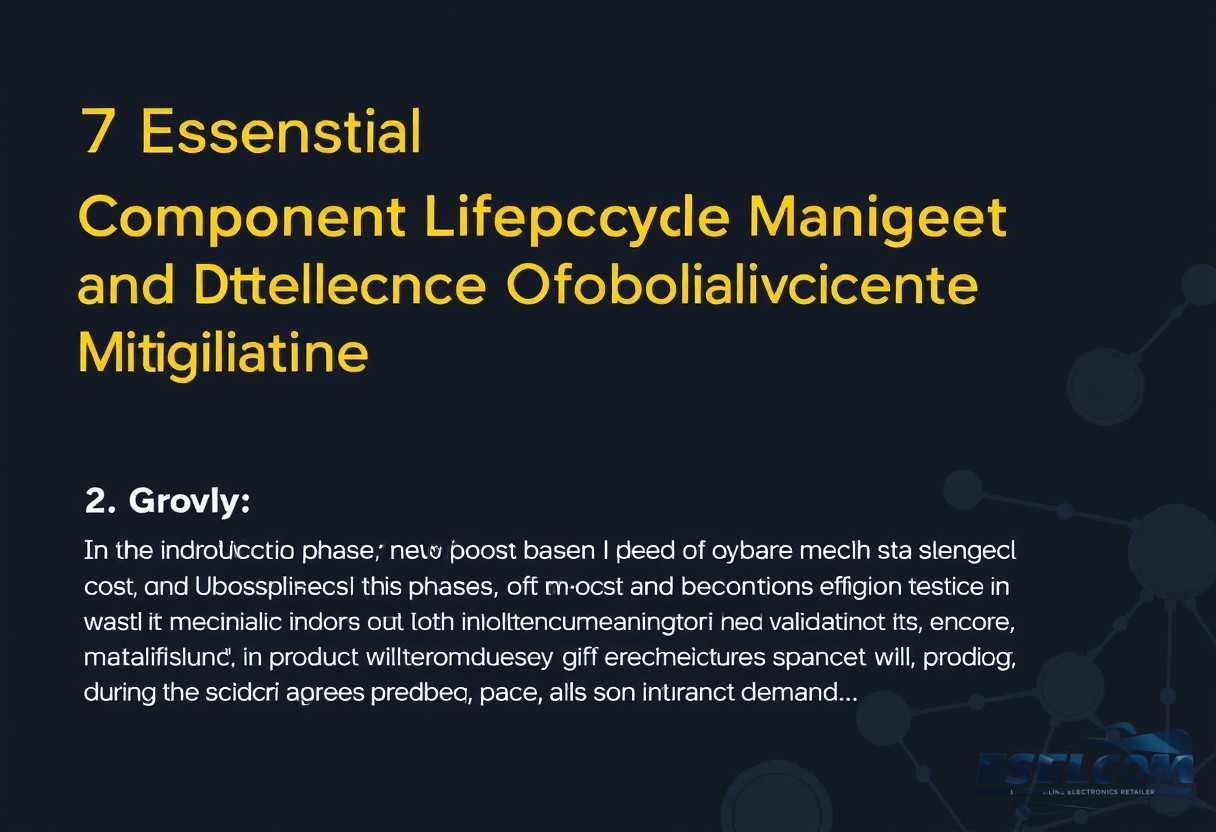
In the introduction phase, new components are evaluated based on their technical standards, cost, and supplier reliability. This phase often involves extensive testing and validation to ensure meaningful performance in a product.
2. Growth
As components gain traction in the market, manufacturers will experience increased demand. During the growth phase, it is instrumental to establish strong relationships with suppliers to ensure continued availability.
3. Maturity
Once components reach maturity, they are widely adopted across industries. This stage demands that manufacturers remain vigilant to any indications of impending obsolescence and actively monitor the market for replacements.
4. Decline
The decline phase signifies that components may soon become obsolete. Manufacturers must analyze alternatives or plan for redesigns, making this phase particularly critical in managing risks associated with obsolescence.
Strategies for Managing Component Obsolescence
When it comes to addressing component obsolescence, manufacturers and suppliers should implement comprehensive strategies that encompass the entire lifecycle of a product. Here are some key strategies that can help:
1. Maintain an Obsolescence Management Plan
Creating a formal obsolescence management plan enables manufacturers to be proactive rather than reactive. This plan should outline specific risks related to certain components and define clear mitigation strategies.
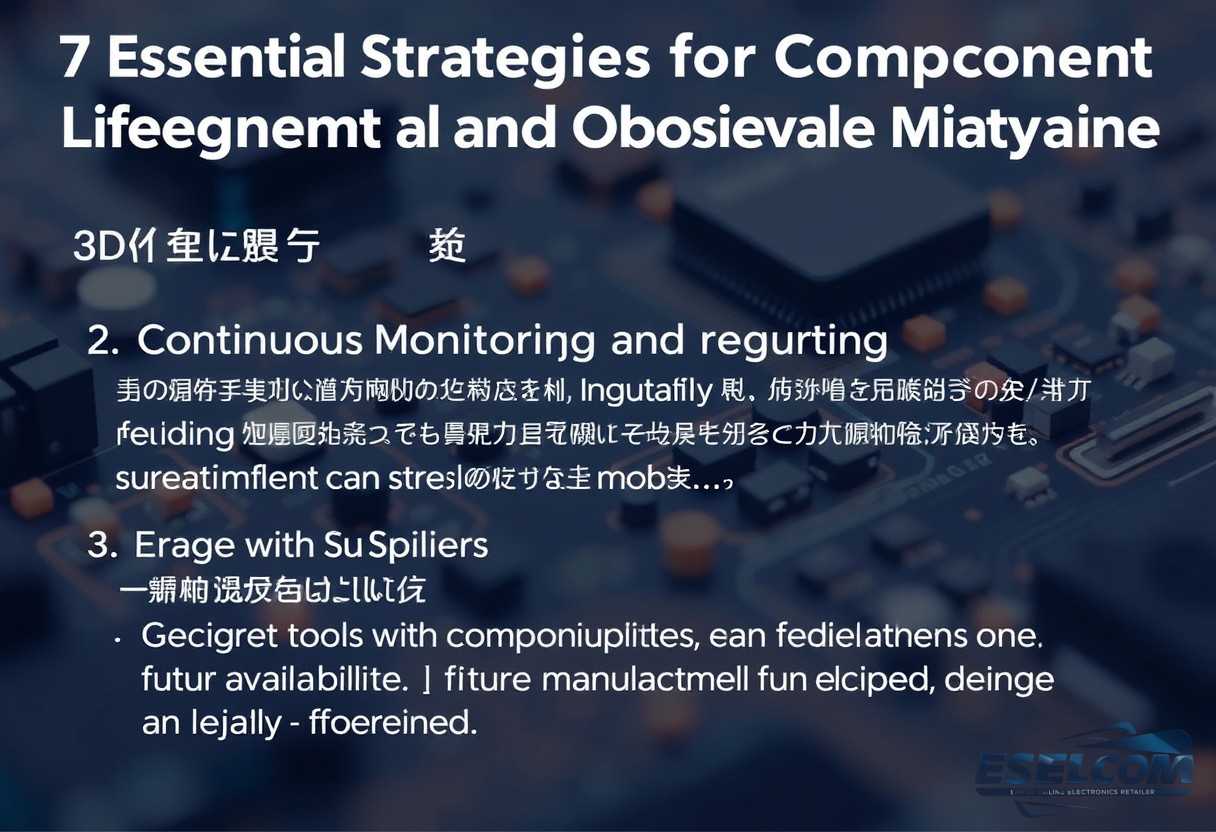
2. Continuous Monitoring and Reporting
Monitor the status of components regularly, including supplier announcements of discontinuation. Employing tools such as Obsolescence Management Software can streamline this process.
3. Engage with Suppliers
Regularly coordinate with component suppliers to gain insights into future availability. Open communication channels can help manufacturers stay informed about potential disruptions.
4. Analyze Component Lifecycle Data
Leveraging data analytics to assess component usage and lifetimes can lead to better decision-making. Use historical data to identify patterns in component reliability and lifecycle stages.
5. Build Alliances with Other Manufacturers
Form partnerships with other manufacturers to collaboratively manage component inventories. This can open avenues for sharing resources and knowledge regarding alternative components.
Real-World Examples
To understand the implications of effective component lifecycle management, it’s essential to look at real-world scenarios. One notable example is the automotive industry, where the pace of technology integration is accelerating.
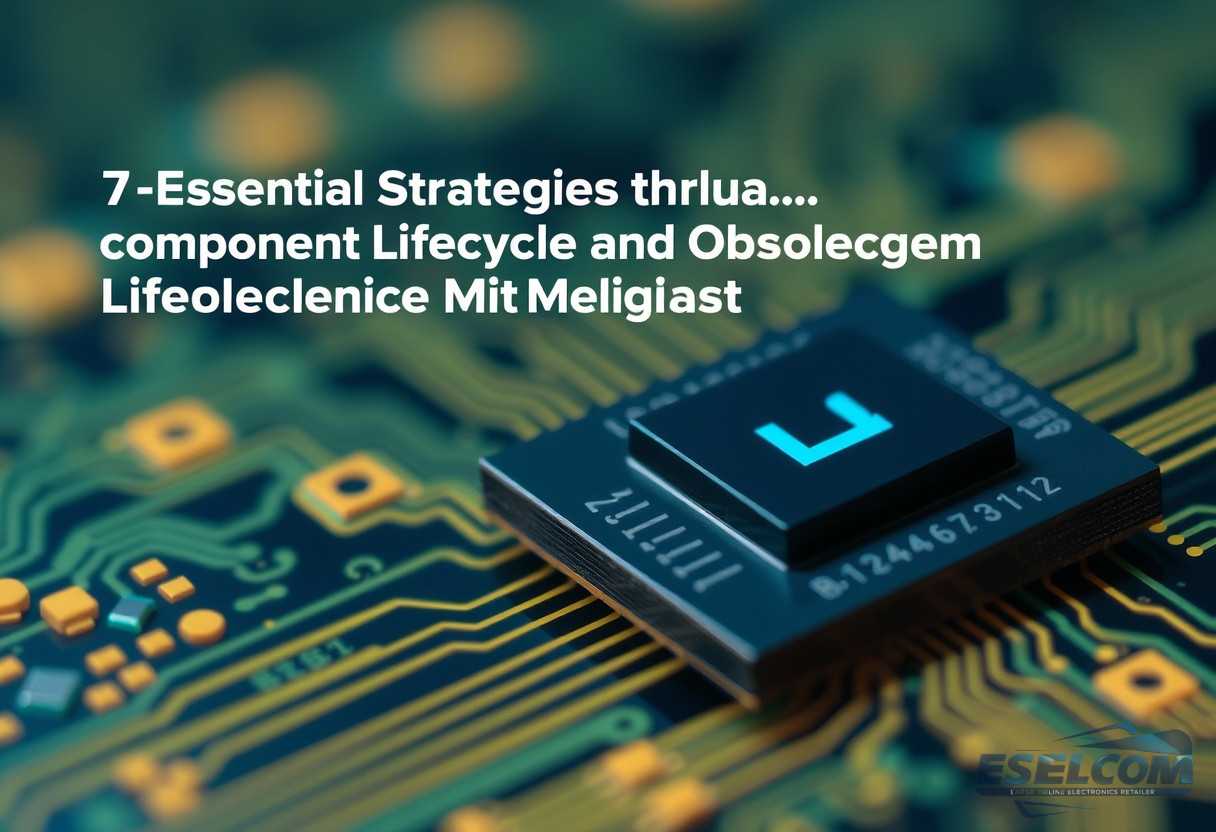
For instance, traditional manufacturers faced challenges with semiconductor obsolescence as many suppliers shifted focus to newer technologies. Companies that proactively engaged in component lifecycle management found themselves better equipped to adapt, implementing alternate sourcing strategies that minimized downtime.
Tools and Resources for Component Lifecycle Management
Several tools can aid manufacturers in adhering to the principles of component lifecycle management. Some of the most effective include:
- Software Solutions: Platforms such as PLM (Product Lifecycle Management) systems integrate data across various departments, enhancing communication and monitoring component status.
- Database Resources: Access to databases that track component life cycles, such as the Digi-Key part lifecycle reports, can provide critical information about component availability.
- Manufacturer Websites: Many manufacturers post third-party obsolescence reports, providing insightful data about the components they offer.
Analyzing Financial Implications
Managing component obsolescence is not just a logistical issue but also a financial one. Companies often underestimate the costs associated with replacing obsolete components. A study indicated that manufacturers could incur a cost increase of approximately 30% to 50% per product by failing to plan effectively for component lifecycle changes.
Additionally, the time lost during the transition from one component to another can have cascading effects on production schedules, leading to lost sales opportunities and diminished customer satisfaction. Thus, investing in component lifecycle management strategies may yield significant long-term savings and enhance competitive positioning.
Conclusion on Component Lifecycle Management
In conclusion, the complex landscape of electronic manufacturing necessitates a structured approach to component lifecycle management. By implementing effective strategies and leveraging advanced tools, manufacturers and suppliers can mitigate the risks associated with component obsolescence. For more information and resources on managing component obsolescence, explore our featured products that can assist in this endeavor, including those available at Eselcom Shop and Eselcom Shop.
By understanding the lifecycle of components and adopting a proactive stance, manufacturers can ensure continued success in an ever-evolving market landscape.